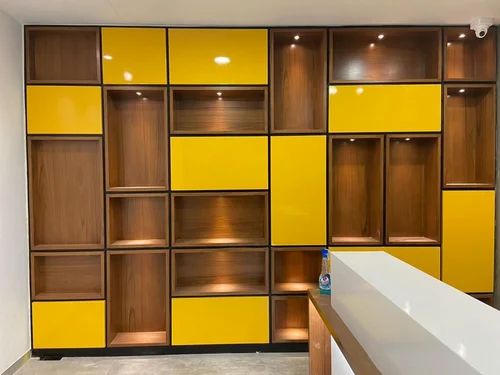
Industrial furniture and fixture repairs are vital for maintaining a safe, productive, and efficient industrial environment. A damaged or malfunctioning piece of equipment can lead to costly delays, safety concerns, and significant productivity losses. This comprehensive guide explores the importance of industrial furniture and fixture repairs, outlining the different types of repairs, best practices, and how to choose the right professionals. This article will cover identifying common problems, choosing appropriate repair methods, and optimizing your maintenance schedule.
Identifying Common Problems with Industrial Furniture and Fixtures
Spotting Issues Early
Industrial furniture and fixtures are subject to relentless use and exposure to harsh conditions, leading to inevitable wear and tear. Early identification of potential problems can prevent costly replacements and ensure worker safety. Regular inspections are crucial for maintaining the safety and efficiency of your operations. A proactive approach is much more cost-effective than reactive repairs. By addressing issues early, businesses can avoid larger problems down the line. Many issues, such as loose fasteners, damaged components, or worn-out wheels, can be identified during routine checks. The sooner you detect these problems, the sooner you can take steps to prevent further damage. Regular visual inspections are a great starting point.
Common Types of Damage
Common issues include damaged legs, broken or cracked surfaces, worn-out wheels, and faulty mechanisms. Identifying these problems early can prevent more significant structural damage. For example, a broken leg on a heavy-duty shelving unit can lead to a collapse and potential injury. Likewise, worn-out casters on a mobile workstation can cause it to tip over easily. Furthermore, malfunctioning electrical components in equipment can pose electrical hazards.
Selecting the Appropriate Repair Methods
Repair vs. Replacement
Careful consideration must be given when assessing whether to repair or replace industrial furniture and fixtures. Repairing damaged items is often the more economical solution, especially when the damage is localized and repairable. However, extensive damage or safety concerns may necessitate replacement. For instance, repairing a chipped paint job might be relatively simple, whereas replacing a completely damaged structural member may be necessary. Assess the cost-benefit ratio thoroughly. Repairing a damaged piece of equipment, or a fixture, is often a more economical approach than replacing it, if possible. A careful examination will help decide if repair is possible or if a replacement is the only viable option. If replacing, be sure to choose a high-quality replacement part or piece that will function as well as the original.
Specialized Tools and Techniques
Specific tools and techniques are required for various repairs. For example, welding or metal fabrication expertise might be needed for structural repairs, while specialized mechanisms may be necessary for high-impact parts. Identifying the appropriate technique for each repair is paramount to successful outcomes. Using the right equipment is essential for optimal outcomes and preventing further damage. For instance, replacing a worn-out part might require specific tools. These specialized tools are generally available from commercial suppliers, and often require training to operate them properly.
Choosing Qualified Repair Professionals
Vetting Repair Contractors
Selecting qualified and reliable repair contractors is crucial for successful outcomes and prevents further complications. Look for certifications, licenses, insurance, and reviews to gauge their expertise and trustworthiness. It is important to choose a contractor with a proven track record of success. A reputable contractor can provide reliable repairs, and their experience and knowledge can lead to cost-saving and time-efficient solutions. Ask for references from previous clients or check online reviews. This due diligence ensures the job is done correctly and to a high standard.
Importance of Experience
Experience plays a vital role in determining the effectiveness of the repair. A knowledgeable contractor can quickly diagnose problems, select the best repair methods, and ensure long-term reliability of the equipment. Experience is an invaluable asset for any professional dealing with complex repairs, where a nuanced understanding of materials, techniques, and safety guidelines is crucial. Don’t hesitate to ask contractors about their experience with similar types of repairs and equipment before entrusting them with your valuable assets.
Optimizing Your Maintenance Schedule
Proactive vs. Reactive Maintenance
Implementing a proactive maintenance schedule is essential for minimizing costly repairs and ensuring worker safety. A proactive approach involves scheduled inspections, preventative maintenance tasks, and routine replacements. In comparison, a reactive approach waits until problems arise, resulting in unexpected costs and potential downtime. A proactive approach is usually more cost-effective in the long run and allows for better management of your resources.
Regular Inspections and Maintenance
Regular inspections are crucial to identify and address potential problems before they escalate into major repairs. These preventative measures save you time, money, and potential hazards to your employees. Scheduled maintenance tasks, such as lubrication of moving parts, cleaning, and tightening of fasteners, extend the lifespan of your industrial furniture and fixtures. Regular inspections ensure that all safety precautions are followed and help to mitigate potential hazards to employees.
Case Studies and Statistical Data
Real-world Examples
Numerous case studies highlight the benefits of proactive industrial furniture and fixture repair practices. A company that implemented a regular maintenance schedule experienced a 25% reduction in repair costs and a 15% improvement in worker productivity. By addressing minor issues promptly, they avoided more costly, extensive repairs that might cause unforeseen downtime. Proactive maintenance programs also help prevent breakdowns during peak production times. By maintaining equipment with careful monitoring and upkeep, you are far less likely to encounter major problems.
Industry Statistics
Statistics reveal a strong correlation between regular maintenance and reduced downtime and improved efficiency. Studies suggest that companies with comprehensive maintenance programs experience significantly lower repair costs and fewer safety incidents. The cost-savings and improved efficiency make a strong case for implementing proactive preventative maintenance practices.
In conclusion, maintaining industrial furniture and fixtures is crucial for operational efficiency and safety in any workspace. By addressing repairs promptly and employing the right techniques, businesses can avoid significant downtime and potential hazards. Implementing a proactive maintenance schedule and leveraging qualified professionals ensures longevity and optimal performance. To learn more about industrial furniture and fixture repair services, contact us today for a free consultation.